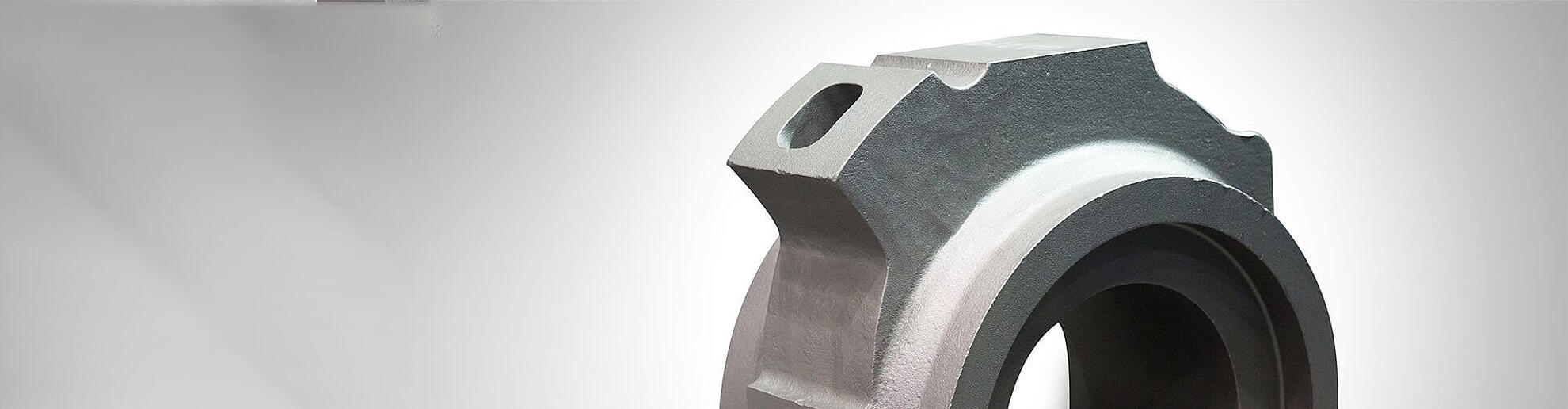
Your specialist for casting and metal processing
The Silbitz Group is a renowned company of the metal and casting processing industry. One of our specialist fields is the casting of iron parts in different sizes. The weight spectrum of our cast parts ranges from 10 kilogrammes through to an impressive 45 tonnes. We use modern equipment at three locations for the casting of components. Here, we are able to meet your demands by offering casting as well as steel and iron casting.
Foundry and casting processing – our locations
The Silbitz Group has a total of three foundry plants: The are location in Silbitz , and in Košice and in Zeitz. All our locations are equipped with the latest technology and quickly and reliably meet the requirements of your casting. In doing so, there are minor differences in the equipment in the different locations. In order to produce your casting, our locations have the following foundry plants:
Our main location in Silbitz has a moulding facility with a chamber size of 1000 x 800 x 350/350 [mm], as well as a mechanical manual casting facility with the chamber dimensions 2600 x 1400 x 800/800 [mm]. Furthermore, we have a hand moulding facility for the production of manually produced castings in the sizes 4000 x 4000 x 1500/1500 [mm].
At our Košice location we also have a finished casting system with the dimensions 1000 x 800 x 300/300 [mm]. This is slightly smaller than our casting facility at our headquarters. Furthermore, here you will also find a hand moulding facility for casting work. It’s dimensions are 5000 x 3000 x 1500/1500 [mm] and it is the second largest system of this type that we have available.
An additional hand moulding facility is maintained at the Zeitz location for work with casting. This is purely a hand moulding facility and can manufacture cast parts with the dimensions 5500 x 5500 x 2500/2500 [mm] or 6600 x 4800 x 3000/3000 [mm] and is therefore, the largest system in our group.
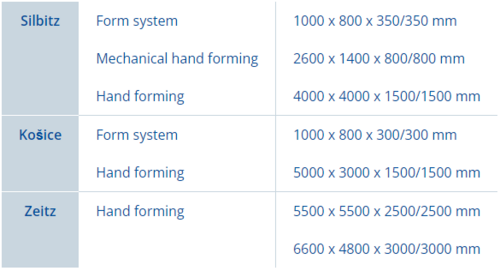
We have 11 different smelting and annealing furnaces available for the production and processing of castings. Our largest annealing furnace has an internal dimension of 6m x 12m x 3m and is large enough to be able to re-treat the aforementioned cast parts without any problems. Furthermore, we are also responsible for “commission-annealing orders”.
Overview:
3 variants are available for the hardening of the casting:
- Quenching “water” (vat with 40m3 volume)
- Quenching “oil” (vat with 40m3 volume)
- Quenching media “moving air” (cooling chamber / ventilators with a maximum loading of 60t)
Testing possibilities of the casting
We have test procedures available to determine all established material characteristics for castings.
- Emission spectrometer for the chemical analysis and determination of O2 + N2
- Thermal analysis of GGG materials
- Material testing to determine the mechanical characteristics at room temperature as well as at high and low temperatures.
- Stationary and transportable hardness testing
- Metallographic devices for the structural evaluation
- 3D measurement and mark-out machine to test the geometry
- X-ray and isotope technology
- Ultrasonic test instrument
- Testing according to the echo impulse procedure
- Acoustical logging
- Wall thickness measurement
- Crack detection instrument for magnetic particle testing with AC and DC current up to 10,000 A amperage and dye penetration processes
- Positive material identification with a transportable spectrometer
- Surface test for surface roughness
Cast for pistons
In special spheroidal graphite iron with high demands based on the
- tightness of the structure,
- uniformity of the micro-structure, particularly the graphite constituent and the
- constructive design based on the cooling effects.
The production of pistons takes place in the diameters of 160 - 640 mm.
The special test methods are:
- X-ray
- Crack detection
- Ultrasound inspection and
- Special offshore approvals
Sectoral examples:
- Ship building
- Compressor construction
- Stationary generators and transformers
- Construction machines
Casting for turnout systems
These include spheroidal graphite iron in the materials.
- EN-GJS-400-15
- EN-GJS-400-18 LT
- EN-GJS-600-3
The production is carried out for the rail shapes S 49, S 54 and UIC 60 as well as special designs in complete turnout sets or individual parts.
Deliveries of the casting are machined ready to fit according to the acceptance test specifications of the DB. Surface refinement is possible. The main consumers are turnout manufacturers and rail companies.
Cast for brake discs
Brake discs for rail vehicles are extremely high quality cast parts with the highest demands and requirements in the materials grey iron, spheroidal graphite iron and cast steel particularly based on the
- high level of uniformity of the micro-structure to achieve an optimal abrasion wear.
The casting for brake discs takes place in the diameters of 300 - 1100 mm.
Special acceptance test specifications:
- X-ray
- Crack detection
- Ultrasound inspection
- Approval of the Deutsche Bahn as a brake disc foundry
Areas of application of these brake discs are rail vehicles with different loads and speeds.
These include spheroidal graphite iron in the materials.
- EN-GJS-400-15
- EN-GJS-400-18 LT
- EN-GJS-600-3
The production is carried out for the rail shapes S 49, S 54 and UIC 60 as well as special designs in complete turnout sets or individual parts.
Deliveries of the casting are machined ready to fit according to the acceptance test specifications of the DB. Surface refinement is possible. The main consumers are turnout manufacturers and rail companies.

Special acceptance test specifications:
- Ultrasound inspection
- Crack detection
- X-ray test and
- Country-specific standards
Areas of application include:
- Chemical industry
- Oil industry
- Gas systems
- Environmental protection technology
The Silbitz Group also carries out a defined heat treatment where necessary. In doing so, the casting runs through different, specific temperature ranges and variations of time as part of the procedure. Different annealing furnaces are available in our company for the heat treatment of the casting. The necessary micro-structural changes of the material are achieved through specific, tried and tested procedures such as austenitising, quenching, tempering or ferritisation. Other procedures for property changes of the casting include isothermal annealing, stress relief annealing as well as soft annealing or ferritisation. By doing so, we are able to produce the casting according to the wishes and requirements.
We can perform surface treatment in order to protect the casting from environmental influences. For this purpose, the Silbitz Group has modern coating chambers available. These are free of dust and work with pre-heated, dry air.
Finally, it must be mentioned that we can deliver the casting so that it is pre-machined or finished and coated. More customers are making use of this possibility of obtaining the casting so that it is ready to assemble.