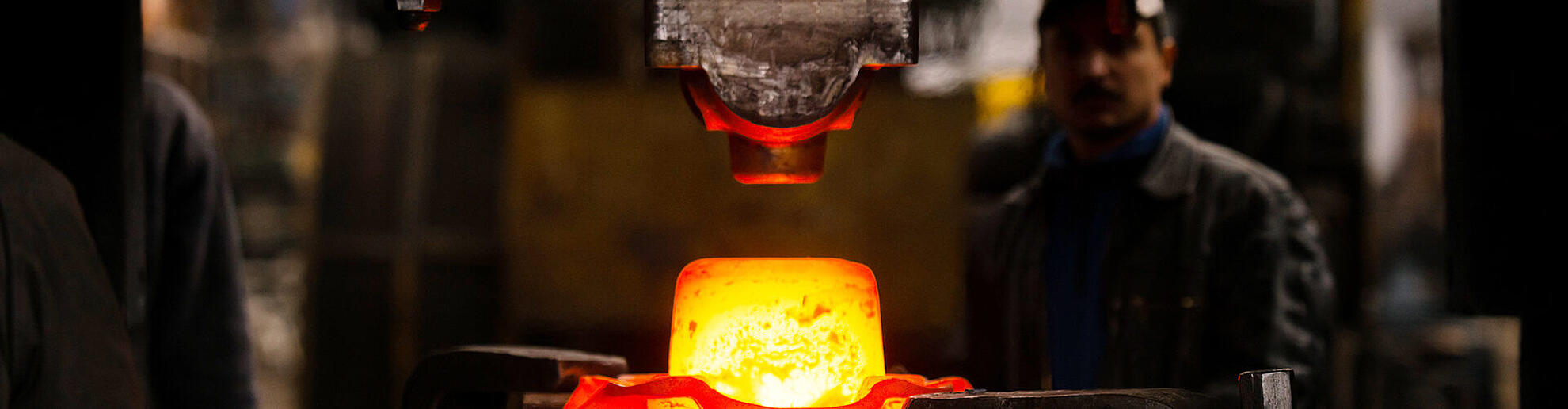
Metallurgical and forging technology – our products
The Silbitz Group has successfully been working in the field of metallurgy and forging technology for many years and offers a wide range of products in these areas. The main products of the metallurgical and forging technology include very high-quality rolling and forging blocks, which are provided for further processing. In addition, ESU electrodes are offered in the highest quality. Selected materials and a sophisticated system technology provide a wide variety of high-quality steel grades, which form the basis for every good metallurgical and forging technology.
Our steel grades of metallurgical and forging technology:
- Heat resistant martensitic steels
- Martensitic stainless steels
- Stainless austenitic steels
- Duplex steels
- Heat-resistant steels
- High speed steels
- Tool steels
And many other qualities on request.
Metal is a material that can be recycled virtually lossless. The entire German steel industry anually adds nearly 20 million tons of steel and scrap iron to the cycle of recycling, which in no way reduces quality. The products from the metallurgical and forging technology of the Silbitz Group also consist of pure metal and one share of scrap metal. The individual products include ingots that can be produced in electric arc furnaces with a bath capacity of 5 to 9 tons. In Vacuum-Decaburitazion or VOD plants, cast ingots with a very high degree of purity and a very low content of oxygen, hydrogen, nitrogen, carbon and sulfur can be produced. There are several annealing furnaces available for heat treatment and preheating of the raw blocks for hot transport within Germany.
Metallurgical and forging technology – highest quality through constant control
We can offer you ingot formats / block casting formats in square and round polygons and block weights from 680 kilograms to 8.5 tons. Likewise, customised molds can be provided and your circulatory material can be remelted for reuse. We guarantee the highest quality on our products in the metallurgical and forging technology by:
- Many years of experience with secondary metallurgical treatment technology
- Control of quality standards in every step of manufacturing
- High quality EMS (emission spectrometer for chemical analysis)
- HYDRIS (direct reading hydrogen measuring system)
- Standardized manufacturing and testing procedures
We are your reliable partner in all areas of metallurgical and forging technology and we look forward to hearing from you.
Excursus: metallurgical and forging technology – then and now
The beginnings of metallurgy are still far removed from the present state of metallurgical engineering or forging technology and go back far into human history. As was the case back then, they have been essential for the development and coexistence of all humankind over millenia. Whole historical epochs were named after the use of the current metal. For example the Copper Age, the Bronze Age of the Iron Age. While in the past, coincidentially found and free-standing ore veins were mined, today they are using highest technology in order to expertly mine above or below the earth’s surface. Initially, metal was turned with simple hand tools into everyday things such as blades, weapons, tools and utensils of all kinds. It was a long way from the start of operation of the first blast furnace. Only then larger quantities of different metal types could be produced. From the 18th century, steel became popular, which significantly influenced the living conditions of mankind again and shaped the name of today’s steel age.