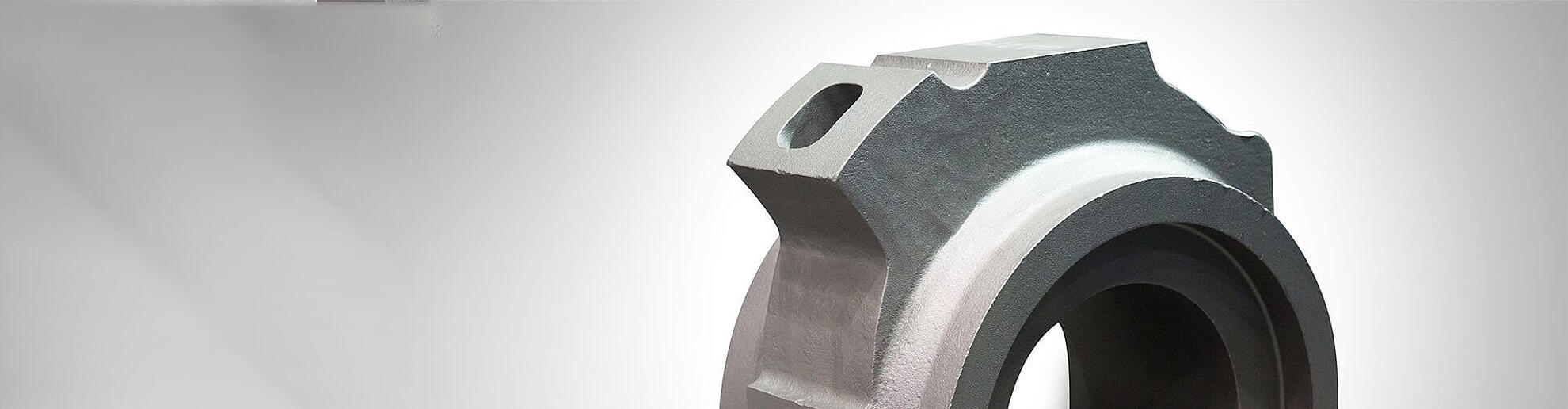
Cast steel from Silbitz
At its main location in Siblitz, the Silbitz Group produces castings made of cast steel in a weight range of between 100 and 9000 kilograms.
Steel castings are the castings made of hundreds of cast steel materials, which have special applications in all sectors. A distinction is made between unalloyed, low alloy and high alloy cast steel, which is distinguished by its properties. The main alloy elements are iron and carbon supplemented by amounts of silicon, manganese, chromium, tungsten, nickel and many other elements. Compared to cast iron, parts made of cast steel have a higher strength level at high elongation values and can also be welded very well.
Special advantages for cast steel and stainless steel castings
Steel casting is ideally suited for heavy duty components in plant and energy machine building. Due to their high tensile strength combined with high elongation values, castings made of cast steel can withstand large, multi-axial loads. For pressure vessel construction, special alloys are required according to DIN EN 10213, since a considerable safety factor must be taken into account. High strength cast steel alloys at the same time also have particularly good weld properties. Steel castings with particularly high compression strength and tensile strength are frequently required, which cannot yet be achieved by the casting process alone. However, a certain relationship of low carbon content (0.02-0.6%) and further alloying elements makes it possible, after cooling in the cast steel mould, by means of special heat treatment methods (for example, tempering - a special hardening and tempering process) to achieve a very favourable combination of properties. Stainless steels are distinguished by their high alloying proportions, which often require the very low carbon contents to be refined in a vacuum. Although corrosion resistance is a large technical area of application, it is not a prerequisite for this designation.
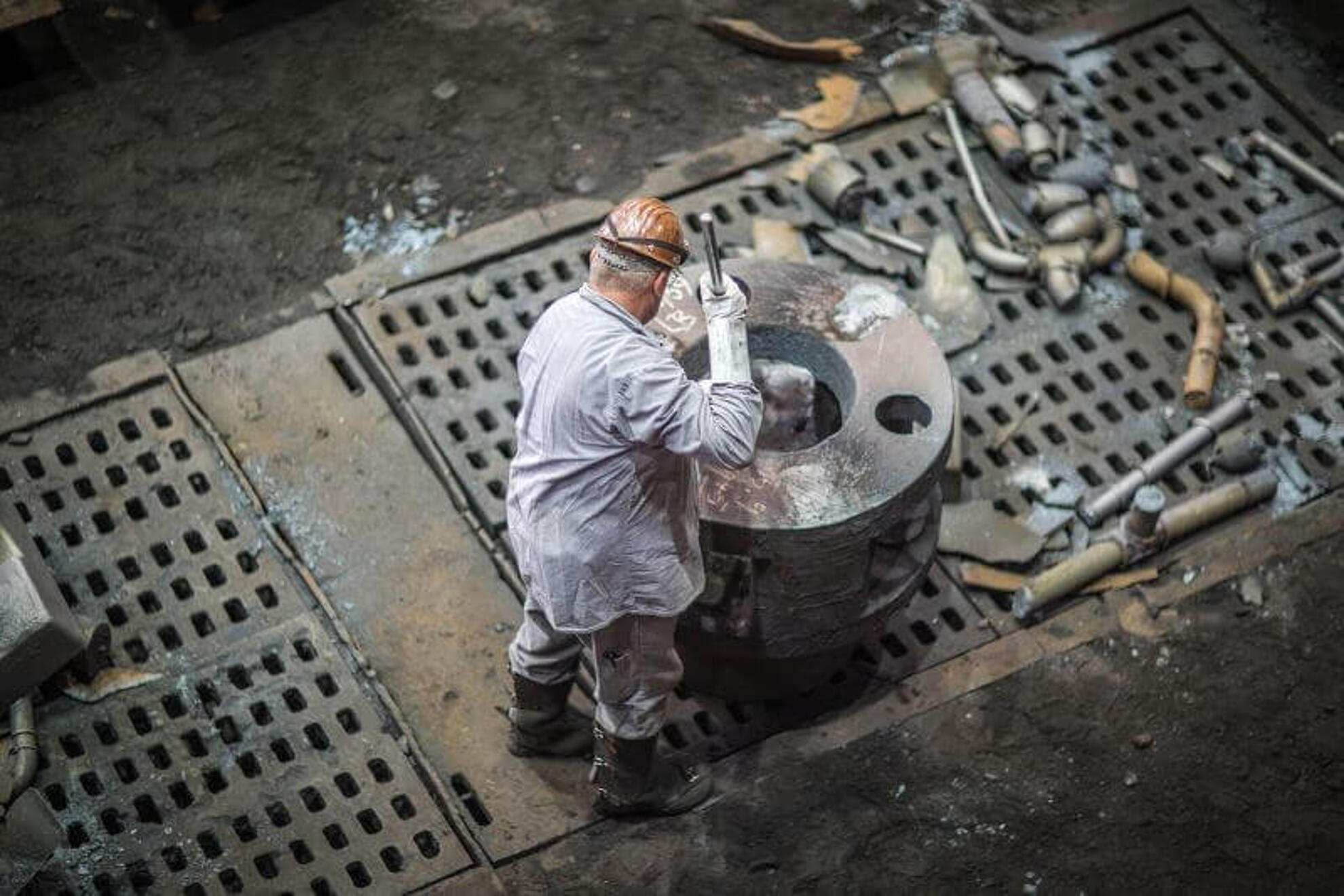
The challenging production of cast steel
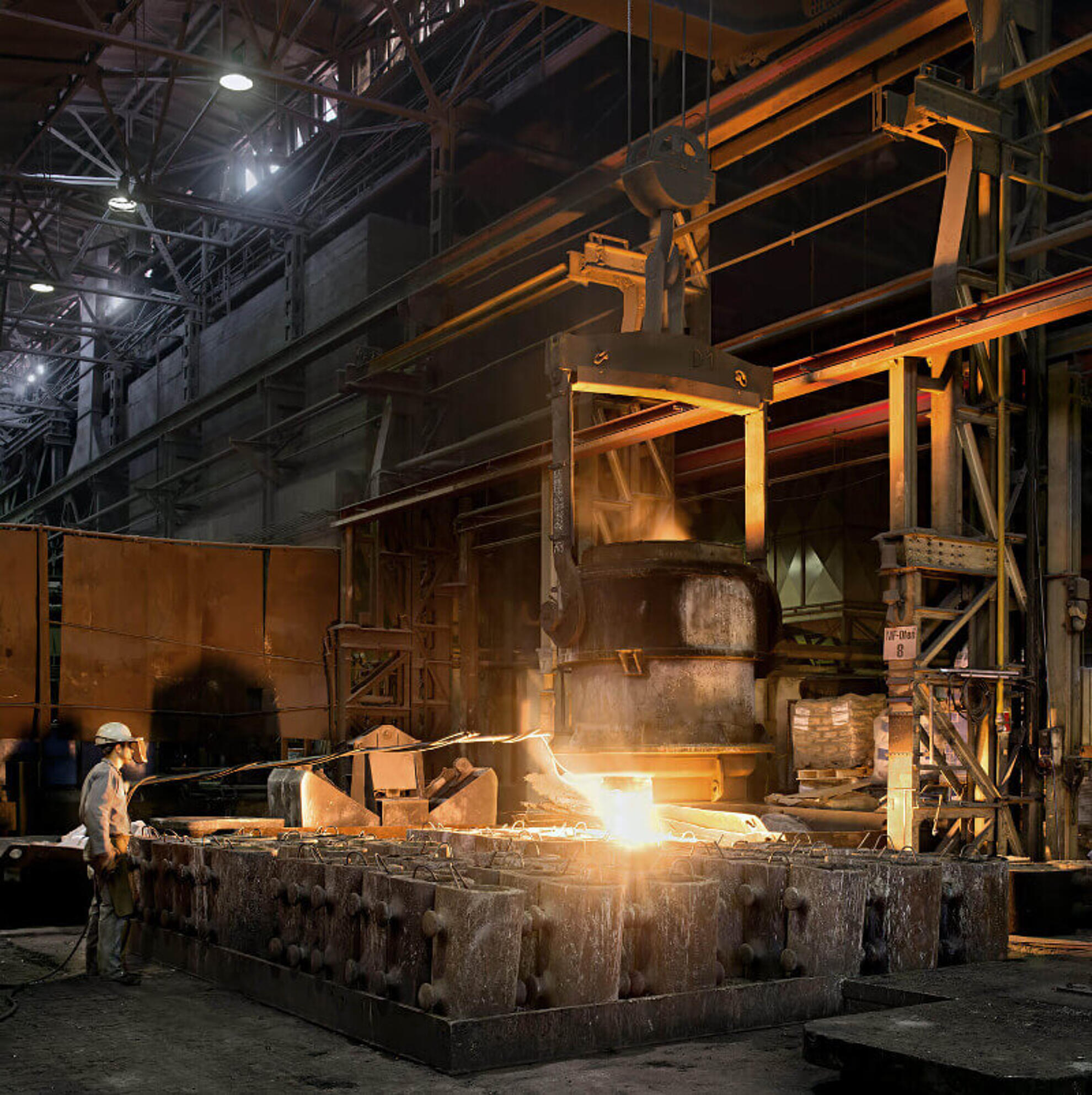
Between the limits of 1520 to 1600 degrees Celsius the pouring temperature of cast steel is substantially higher than that of cast iron alloys. Therefore, the technical requirements for the manufacturing process are more demanding. Melting pans, melting aggregates and their lining must have a very good fire resistance in order to withstand the high temperatures during the manufacturing process. In addition, the shrinkage in cast steel is comparatively high at 2 percent. The casting process results in steel castings, which are initially brittle and coarse in their primary solidification. Subsequent heat treatment (normalization) is therefore necessary in most cases. Nowadays, casting and feeding techniques in the expected filling and solidification processes are pre-calculated with sophisticated simulation software and this forms the basis of model production concepts, which are tailored specifically to each customer's request.With the possibilities of design and contract welding, further application areas are opened up, which the combination of different components with intricate design and different blanks (forging or pipe sections) makes possible.By means of making full use of the resulting steel scrap, the principle of re-usability through the possibilities of using old parts when melting down, is exemplary in the protection of the environment and the ability to recycle.