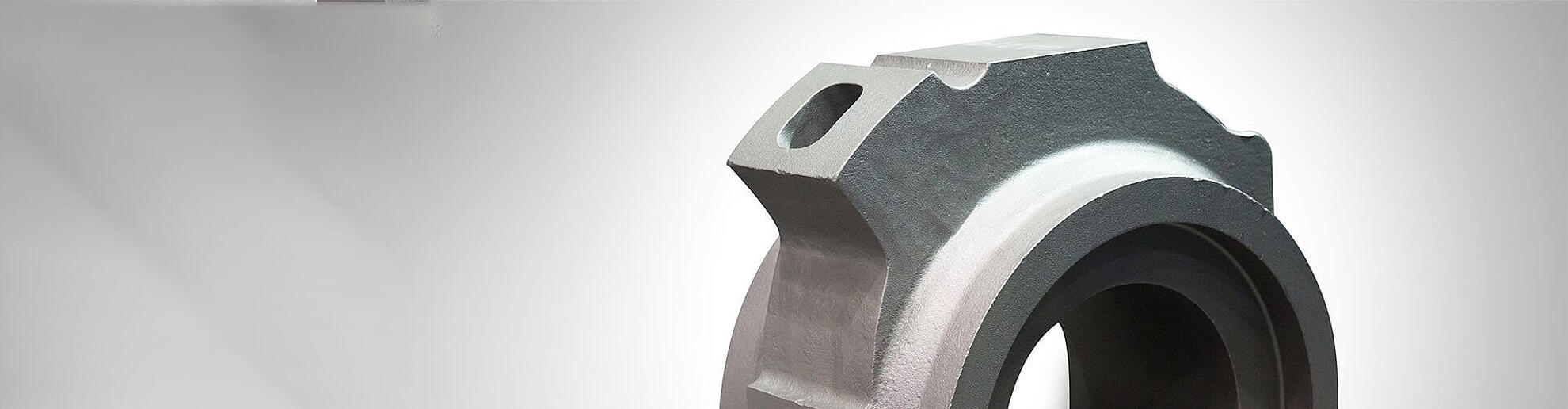
Construction of cast parts
Definition of casting manufacturing
The design of cast parts refers to all processes and production steps associated with mold casting. Castings can consist of different moldable materials that are formed and processed in the casting process. The design of cast parts requires a model (tool), a mold, heating processes and continuous quality control throughout the entire machining process. The term design for cast parts refers to all processes that the material undergoes from its conception to the finished cast product.
Expenses and methods in casting manufacturing
The methods used to design cast parts depend on the metal (material) to be processed and its properties. Mold casting requires various preparatory tasks that enable precision casting and ensure dimensionally accurate castings. Design and simulation precede the actual material casting. After the production of a pattern, the mold and the casting, the parts are mechanically reworked and refined. The subsequent quality control serves to test the end product, which is carried out in individual processes.
Different processes in the concrete casting procedure
Primarily, we differentiate between different moulding processes in casting manufacturing. There are sectors such as static casting production, ingot casting production, continuous casting production etc. Another differentiation is based on the casting manufacturing with disposable moulds or with permanent moulds. The chill casting, the pressure die-casting and the low pressure die-casting or the centrifugal casting are further forming procedures in casting manufacturing. The moulds are made, according to their batch, as permanent or disposal mould, preferably with special kinds of sand. Depending on the casting method, the part has to be finished mechanically, as there are also coarser moulding methods besides the precision casting method. These methods are generally used for the construction of prototypes and single parts.
Casting manufacturing is versatile: innovative casting methods
Which method is the correct one depends on the material and the application area of the finished casting. If the casting is, for example, supposed to be a wear part, a permanent mould will be the most economical solution over the long term. Furthermore, the favored technique will be geared to the shape of the finished casting, which can be produced as a hollow body, a part with notches or as an ingot casting. While the serial casting production will be made with the help of a permanent mould, smaller batches or single castings are produced through less expensive lost moulds.
Casting manufacturing with a comprehensive quality control
During the casting production, the simulation, the model construction and the whole production process, the Silbitz Group as an experienced casting manufacturer is making a comprehensive quality control. By doing so, the economic efficiency and certainty that the casting manufacturing is done precisely in all steps of the process is raised. With over 120 years of experience as a casting manufacturer and developer, we arrange for sustainable quality and a selection of materials, which correspond to the purpose as well as for stable and durable production castings according to the highest quality standards.